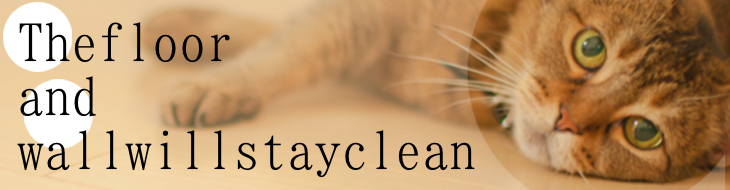
HG Coat is a coating agent that forms a transparent ceramic film.
This film has resistance to UV lights and has superior incombustibility, acid resistance, water nonpermeability, and contamination resistance. Just a thin layer of this film can work as a gas barrier having corrosion resistant property that can protect the foundation.
1. An inorganic coating film that has superior resistance to weather, chemicals, and heat.
2. The hard film has superior wear and abrasion resistances and hard to get scratched.
3. It is a cold-curing coating agent, so it can be applied at the construction site.
4. Graffiti and poster prevention effect (Hg Coat α).
Heated a partially-coated stainless steel plate with a gas burner, and compared the result between the coated portion and uncoated portion. When we stopped burning, the coating film broke due to abrupt cooling, but thanks to the gas barrier property of the film, there was no discoloration of the plate surface by oxidation.
After coating and dry-curing a part of a stainless steel plate, soaked it in hydrochloric acid solution. Only uncoated part was discolored.
Building exterior (painted surface, etc.) | Maintains good appearance for a long time and reduces maintenance burden |
Building interior | Protects and prevents staining of floors, ceramics, and walls. |
Metal | Prevents rust and degradation |
Stone materials, tile joints | Prevents rust and dirt |
Type | HG Coat R (solution 1) |
Color | Very light yellow transparent |
Coating film property | Glossy |
Appropriate coating film thickness | 5~15µ |
Dilution | Isopropyl alcohol (IPA) |
Once mixed, it absorbs moisture and hardens. Therefore please store is in a cool, dark place in a sealed container.
(If stored in a sealed container under low temperature, it will last for a few weeks.)
The coating film itself has resistance to 700℃ heat. Transparent curing agent is also available.
Various types are available for different base materials, applications, and functionalities.
Graffiti prevention type…HG Coat α (two solutions; main agent and curing agent)
Dedicated primer (metal, resin, stone)…RMB-10 (two-solution type: main agent and catalyst)
Type | HG Coat/td> |
Ingredient | Sio2 |
Maximum coating film thickness | ~13µ |
Heatproof temperature (℃) | 700℃ |
Hardness (depends on cure condition) | ~7H |
Specific gravity (25℃) | 1.05 |
Viscosity (CP) | 40 |
PH | 5.0 |
Refractive index (Becke’s line method) | 1.43 |
Volume resistivity (at 25℃, Ω-cm) | 1014< |
Glass components in the solution (%) | 57 |
Diluent* | IPA |
*Diluent is not always necessary. (IPA=isopropyl alcohol)
Touch drying (atmospheric temperature is at 20℃)…2 to 3 hours
Standard curing (Hardness H~2H)…24 hours
Full curing Baking at 150℃ for 30 minutes (this is a rough guide).
(It reacts by normal-temperature long-term curing, but it will be hard for the coating film to be completely inorganic.)
1. Incombustible film formation…Around 40 hours (may slightly differ depending on the film thickness)
2. Solvent resistant film foaming…3 days or more (It reacts to solutions at first, but it will gradually become resistant when dried by heated air or after long-term curing.)
3. Water resistant film forming…Around 24 hours (may slightly differ depending on the film thickness)
Test machine: Super UV Tester W-3
UV irradiation: 90mW RH70%
Dew Cycle:Light/dark 4/2hrs Water Spray 15sec/30min